A Platform management

Work on the field was coordinated through a daily meeting held at 18.00 in the field manager’s office. Similar meetings were held simultaneously on CDP1 and DP2. They were attended by the heads of every department – production, safety, maintenance, inspection and catering. The events of the day were summarised, with the opportunity to ask questions, conduct discussions and solve any problems. This meeting also provided a good occasion to keep all the departments updated about what was scheduled for the following day.
If the maintenance department was going to carry out welding, for instance, the safety team could institute the necessary precautions in the relevant area. Decisions were also taken and notified about how the process was to be managed on the following day – whether the gas flow was to be changed or diverted, for instance.
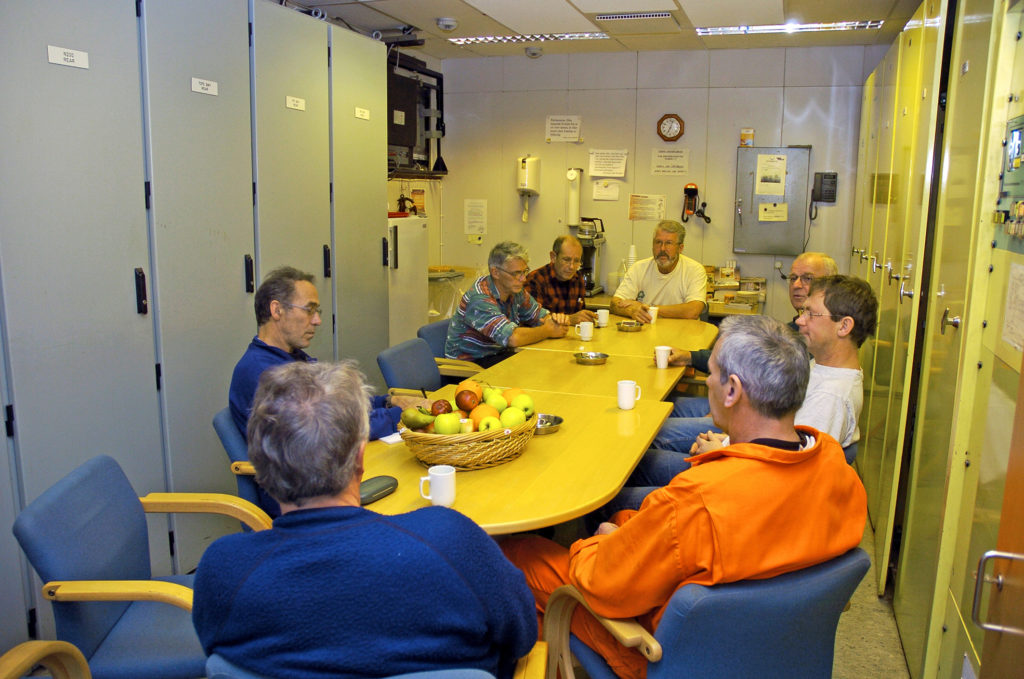
A daily morning meeting was also held to prepare work permits, which were signed by the field manager afterwards. In later years, these orders were handed out in the control room rather than distributed around the platforms. A copy of each permit was retained by the control room, so that its staff was informed about the work to be done.
Everyone on Frigg had a 12-hour working day. A number of jobs were duplicated on both day and night shifts. That applied particularly to production and catering personnel as well as to production operators and communications staff. The tour rotation was initially eight days offshore followed by eight days free on land. This was gradually changed, with the time off steadily extended, and ended up as two weeks offshore and four on land.
The change-over was on Tuesday for the offshore installation managers, Wednesday for the maintenance superintendent and Thursday for the safety supervisor. Staggering the transitions in this way was an attempt to maintain continuity and ensure overlapping between tours. Keeping logbooks also helped to achieve continuity.
Field manager
The field manager on Frigg had overall responsibility for its operation. This person was the superior of the offshore installation managers (OIMs) on CDP1 and DP2, and also acted as OIM for QP, TP1 and TCP2 – the platforms which made up the central Frigg complex. The field manager reported directly to the production department on land and was responsible for all activities on the field – including correct implementation of all Elf’s systems and procedures. Keeping the management of the production department informed about all issues relating to gas output and ensuring that all the offshore departments received the necessary information was part of the job.
An overall responsibility for work performed on the field rested with the field manager, but this person did not exert direct influence over appointments and careers. While the field manager had a small budget, approval had to be secured from land for most spending. A working environment survey conducted in 1980 found that the field manager had responsibility but not authority.
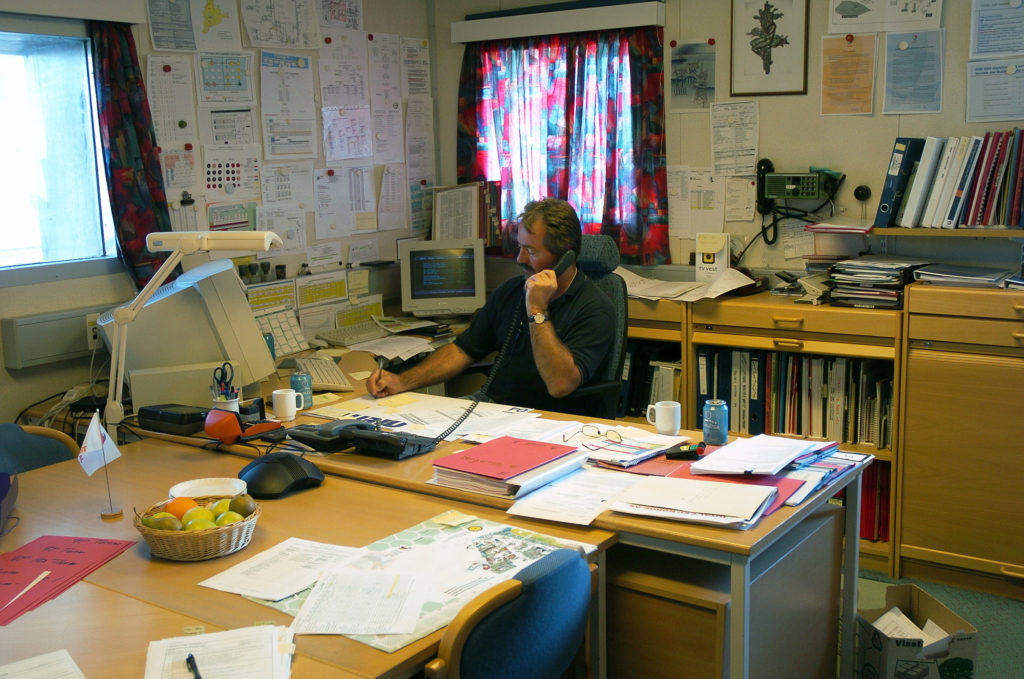
The field manager was assisted by a field secretary on QP, who dealt with administrative issues. In particular, the secretary maintained contact with Dusavik and submitted reports and updates.
Offshore installation managers
The offshore installation manager (OIM) was the senior officer on a platform, with special responsibility for safety and the technical aspects of operations. Frigg operated with two different titles for its OIMs, since it straddled the UK-Norwegian boundary and the regulations for this job differed between the two countries. Under British practice, the OIM was almost comparable with a ship’s captain – personally responsible for operations, and subject to fines if regulations and orders were not observed. Norwegian rules made the operator company responsible for ensuring compliance with law and regulations.
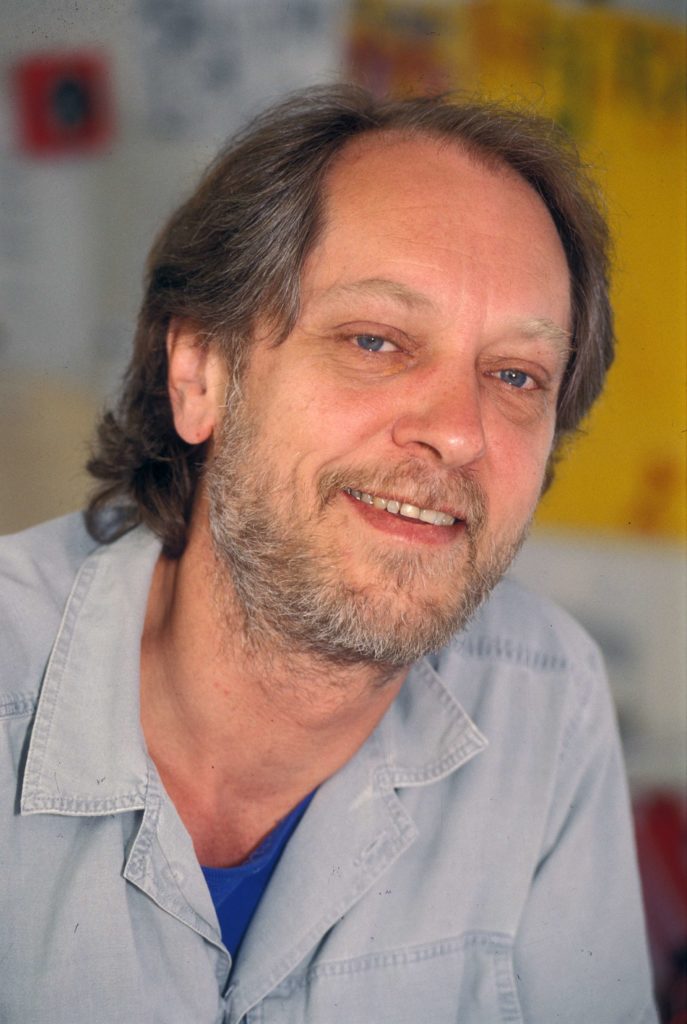
“We reviewed jobs and followed up organisational changes at the evening meetings,” recalls Christian Hansen, an OIM for a number of years, when describing a typical day. “We looked to a great extent at the individuals to see who could work together. As an OIM, you had to be a bit of a social anthropologist. This was an isolated community. It was important to watch out that people weren’t treated differently but nevertheless subject to individual tailoring. Many OIMs served for a long time, and became part of the social scene. The field manager on the central complex was in charge of everything. The OIMs on CDP1 and DP2 nevertheless had a degree of independence and could take decisions in emergencies, for instance.”
Administration superintendent
The administration superintendent had an office on QP and was responsible for the administration department. This person headed work by the catering personnel, the radio operators, the marine coordinators, the heliguards, the fireguards, the security personnel on the helideck, the caretakers, receptionists and helicopter crews. The administration superintendent reported to the field manager and the transport department on land, and kept track of overtime, checked time sheets and so forth.