Well maintenance

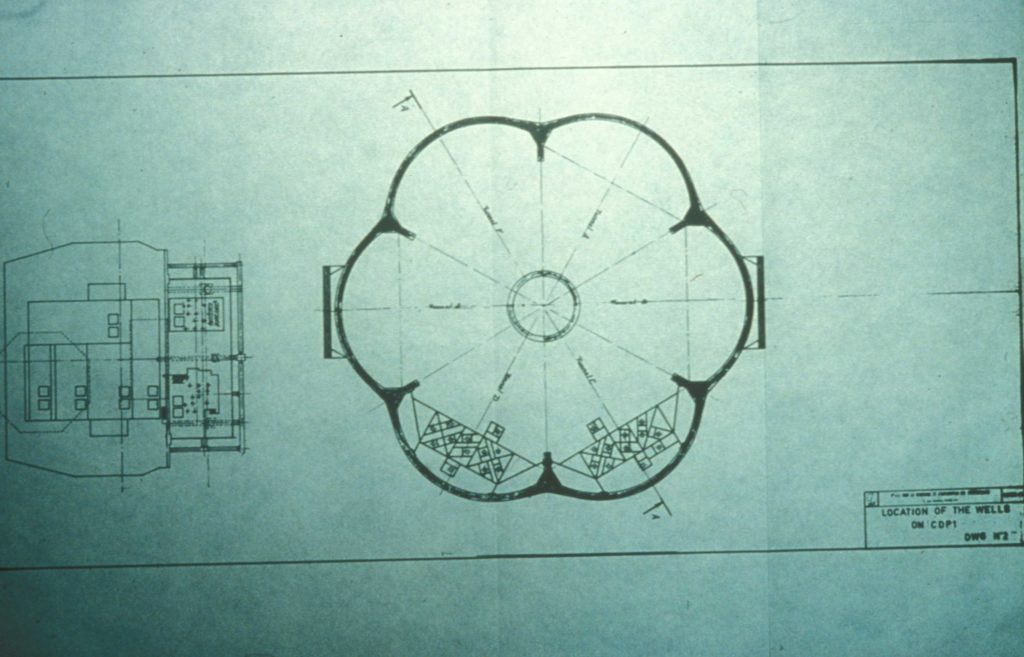
This work was carried out by various drilling contractors, under the management of the drilling department on land. After a well had been drilled, other service companies came out and completed it. These had special equipment for setting sand filters at the bottom of the well and packer elements between the well wall and the production tubing to prevent gas from flowing up this annulus. The wells were then handed over to Elf and the operators on the drilling platforms. Since Frigg gas contained little sand, production from the field was steady. But the wells and production equipment on the platforms nevertheless had to be regularly tested and maintained. The regular maintenance team was primarily responsible for overhauling the topside Christmas tree (valve assembly) and production equipment. Electricians, instrument technicians and mechanics were permanently employed on the platforms. The equipment was tested by the operators, who called out maintenance personnel if irregularities were found.
Well testing
The operators tested the wells regularly. Each well had a dedicated system for such checks. Since gas from each cluster of six wells was collected in a manifold, it was difficult to see if all the wells were producing at their optimum rate. To check production for an individual well, its gas stream was diverted to a dedicated test separator to determine the flow rate. This was done regularly with all the wells. If irregularities were discovered, preparations were made for a well workover.
Light workover
The well was passed to the well department on land. One or other service company would be mobilised, depending on the problem concerned. This could call for a light workover, carried out as a wireline or coiled tubing operation or through corrosion control.
Wirelining meant running a thin cable down to the well to position equipment or carry out work. This could involve setting or retrieving a downhole safety valve installed in the production tubing, opening or shutting the circulation gate valves at the base of the production tubing which are used to kill a well with drilling mud, or measuring pressure or temperature in the production tubing or reservoir. Such operations could also be used to check the tubing for corrosion damage or for cleaning it.
Coiled tubing was another form of well workover operation performed by service companies. Smooth tubes which could be spooled continuously on large drums were used for well clearing or stimulation, fishing operations to retrieve equipment which had fallen down the well, cementing work, various activities relating to sand control, and different kinds of operation to support production.
Heavy workovers
Although sand intrusion proved a minor problem on Frigg, it was not unknown when production began. A screen was accordingly installed at the bottom of each well to remove any sand grains which might enter together with the gas. A heavy workover programme was conducted in the Frigg wells during 1986 and 1987. This called for the use of a derrick to pull out all the production tubing. One motive for this operation was to replace the sand screens. After eight years, however, they turned out to be almost as good as new. Virtually no loose particles had been picked up.
Wellhead maintenance
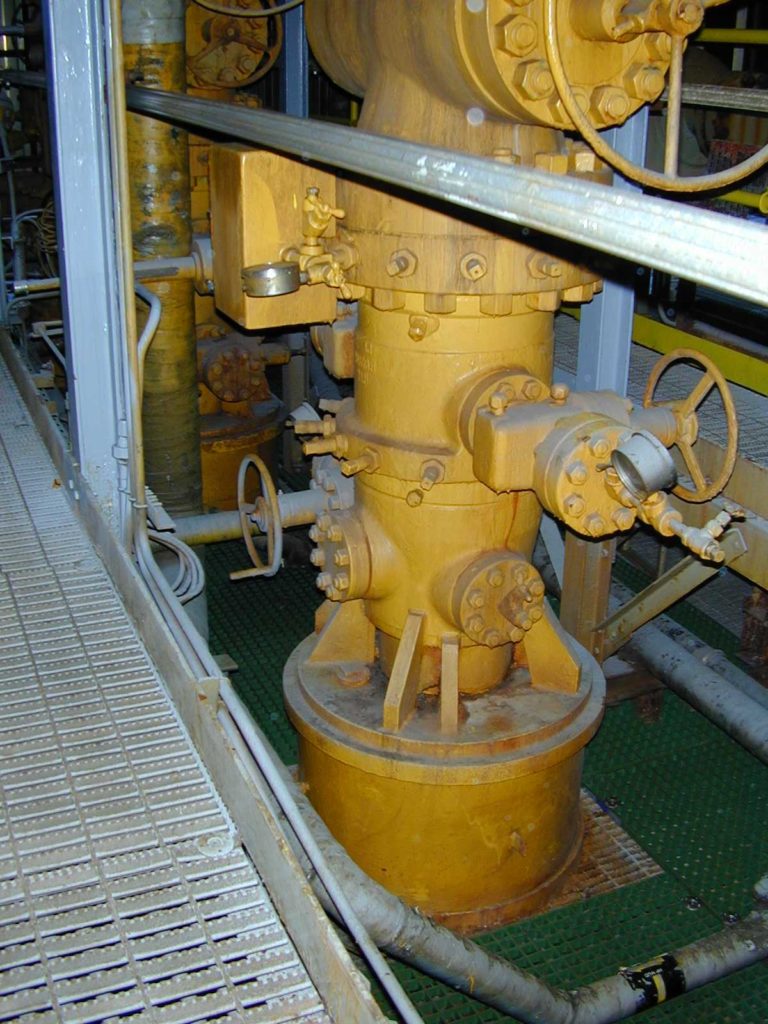
Maintenance and repairs were also needed on the wellheads. The master valve might need to be replaced, for instance. This required the surrounding wells to be shut down and the removal of the whole wellhead before a replacement could be made. The operation was both complex and risky. In 1981, a master valve was replaced for the first time without shutting down the surrounding wells. Carried out on DP2 by McEnvoy, a specialist British company, this job required that the master valve be repaired without any equipment removal. The wellhead was opened in situ and the valve removed. McEnvoy’s approach was to install the replacement components with the aid of a new mechanical tool equipped with a piston. The most difficult aspect of this operation was positioning the replacement units. Only two days were required for the work, compared with the week normally needed if the wellhead had to be lifted out. This meant a substantial reduction in repair costs.