Tørking

Tri-etylen glykol trekker til seg vann slik at gassen som kom ut av toppen på tørkeenheten var tørr. Tørr glykol ble pumpet inn ved toppen av tanken og den våte glykolen fjernet nær bunnen. Fra tørkeenheten gikk gassen til kontrollventiler og målestasjoner før den ble eksportert til Skottland i en 32″ rørledning.
Glycol tørker (Regenerator)
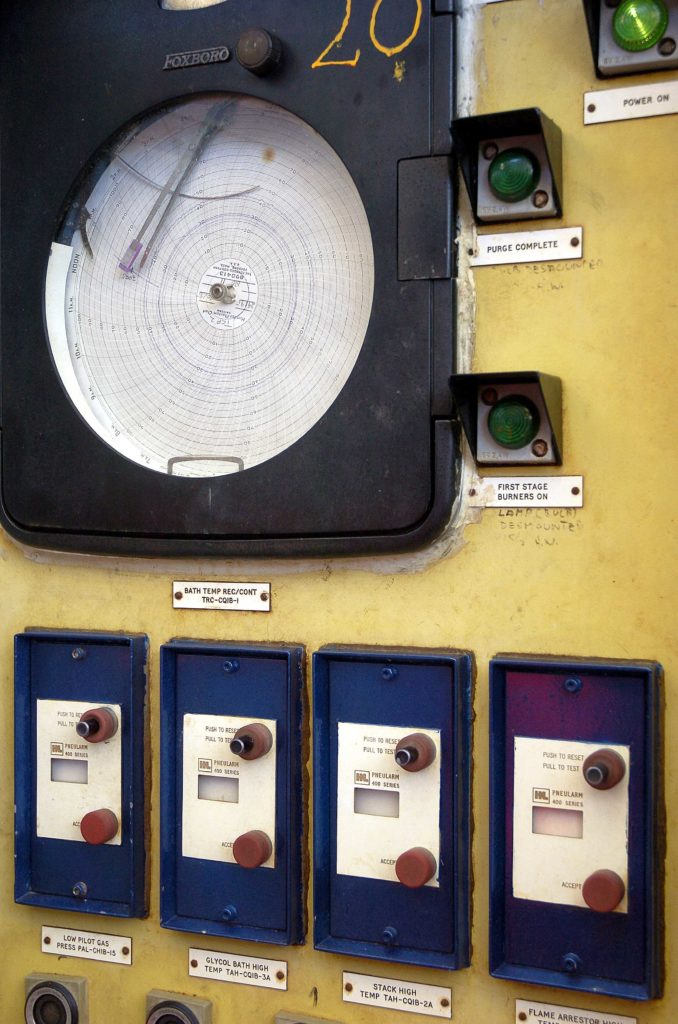
Glykolen som hadde vært brukt i gasstørkeren hadde tatt opp i seg vann. For å kunne bruke glykolen om igjen måtte dette vannet fjernes. Dette ble gjort i glykoltørkeren der glykolen ble varmet opp slik at vannet dampet av.
Våt glykol ble først sendt til en separator der eventuelle hydrokarboner ble fjernet. Neste steg var en varmeveksler og en glykol varmeenhet der glykolen ble varmet opp til 204°C og vannet dampet bort. I varmeveksleren ble glykolen avkjølt og ført til en samletank for deretter å bli pumpet tilbake til gasstørkeanlegget.
Temperaturen i varmeenheten var avgjørende for hvor tørr glykolen var, og denne igjen styrte gassens tørrhet. Ved å endre temperaturen i varmeenheten kunne en derved kontrollere gassens tørrhet.
Operatør tørking
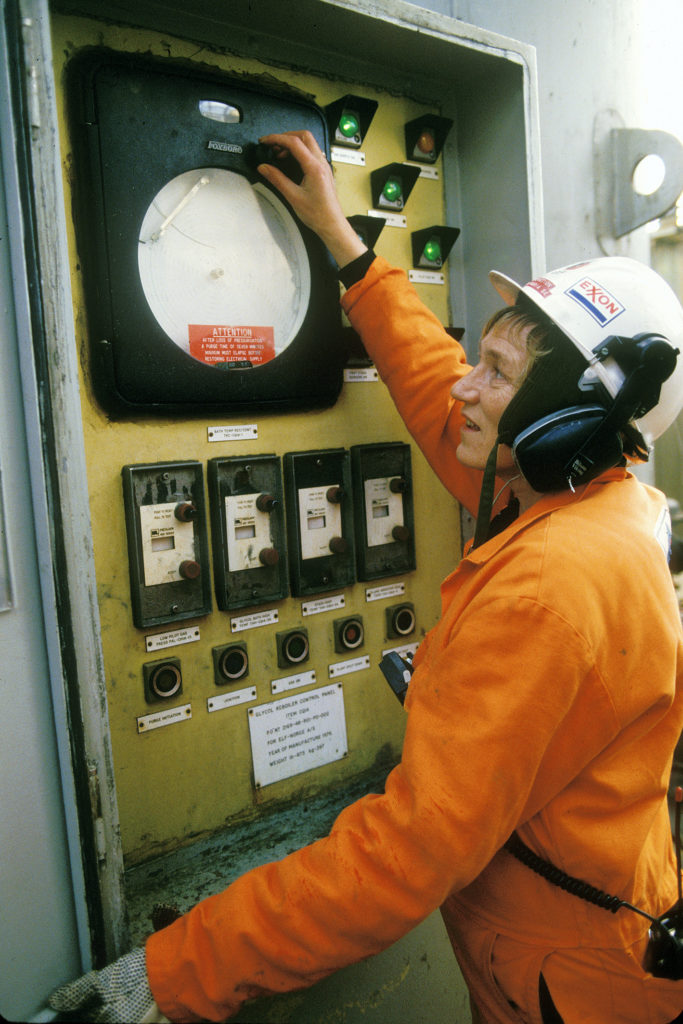
Etter at gassen, kondensat og vann var separert, gikk gassen inn til glykolkontaktoren, hvor den ble tørket for resten av vannet. Gassen kom inn i bunnen av tårnet og boblet opp gjennom glykolen som kom inn på toppen. Glykol, som er et produkt fra karbohydrater og sammenlignbart med frostvæsken som brukes i radiatoren på en bil, har stor evne til å binde til seg vann. Gassen steg opp igjennom flere kar hvor glykolen hadde samlet seg slik det ble mest mulig kontakt mellom glykol og gass. Når gassen kom ut igjen på toppen, var den helt tørr og kunne sendes i rørledningene til St. Fergus. Glykolen som kom ut i bunnen av tårnet, ble varmet opp og tørket i en glykolregenerator, for så å brukes om igjen.
Operatørene, sammen med en laborant, sjekket disse operasjonene flere ganger om dagen. Prøver av glykolen ble tatt for å se kvaliteten. Hvis vannmengden var for liten, viste det at glykolen ikke lengre klart å ta opp nok vann. Det kunne bety at den var slitt og måtte byttes ut. Operatørenes oppgave var å sikre at gassen hadde den rette tørrheten før den ble sendt i rørledningene til Storbritannia. Gassens tørrhet ble bestemt ut fra glykolens tørrhet og hvor mye vann glykolen hadde mulighet til å binde til seg. Tørrheten på glykolen ble justert gjennom temperaturen på glykolregeneratoren.
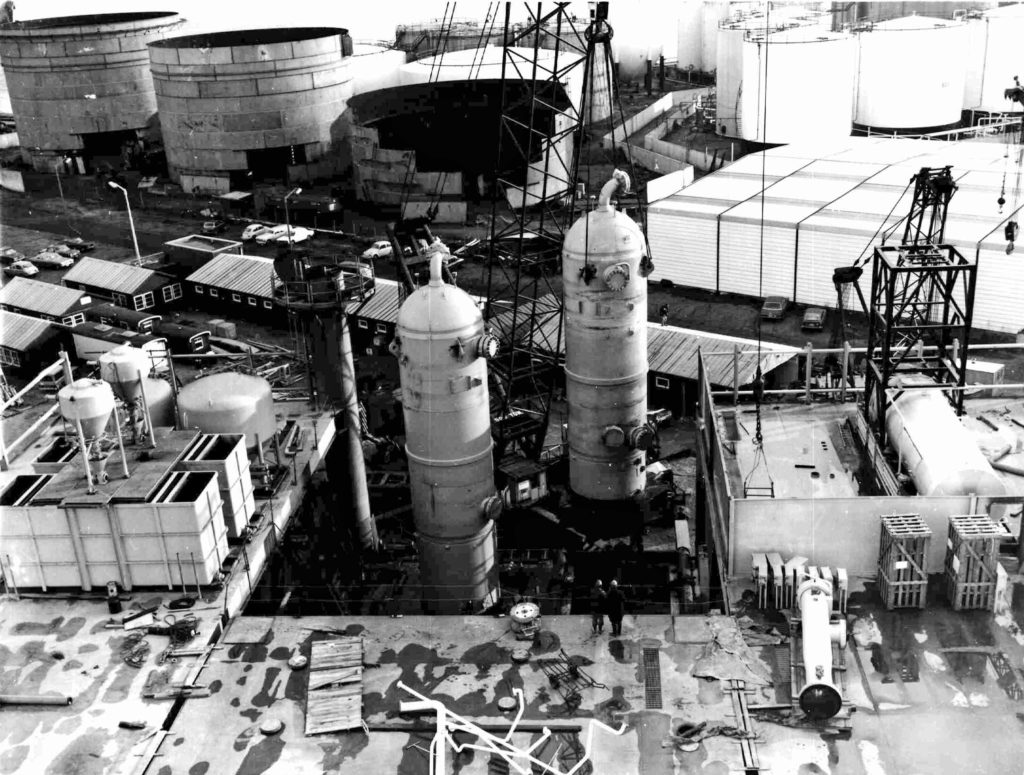
Det var tre operatører på hvert skift på prosessplattformene som jobbet i team. En hadde ansvaret for kompressorene og en for resten av prosessen og en for gasstørkingen. Gasstørkingsdelen på Frigg var en travel jobb med mange små justeringer, og det trengtes en egen operatør med ansvaret for hele glykolsystemet. Operatøren som hadde ansvaret for gasstørkingen, overvåket prosessen ute i prosessmodulene, hvor de fysisk etterså utstyret.