Kontrollrom på QP

- Å kontrollere strømningsraten fra hver produserende brønn på CDP1 og DP2 og den totale gass-strømmen til Skottland
- Å kontrollere strømningsraten gjennom hver prosesseringsenhet på prosessplattformene TP1 og TCP2
- Å kontrollere trykket i rørledningene til Skottland
- Å overvåke temperatur, trykk, strømningsrate og andre prosess parameter i alt utstyret på alle plattformer
- Å følge med på prosessen for å kunne gjøre justeringer ved indikasjon på unormale tilstander og ved alarmer.
- Å ha oversikt over alle ventiler og pumper slik at de rette inngrepene i prosessen kunne gjøres.
Et mimikkpanel på veggen i kontrollrommet viste alt prosessutstyr og alarmlys samt om ventiler og pumper var avstengt eller i drift. Under mimikkpanelet var det måleinstrumenter og skrivere for alle kontrollpunktene for temperatur, trykk, strømningsrate osv. Fra kontrollrommet kunne en også kommunisere med personell på de andre plattformene slik at en kunne gi ordre om ting som måtte gjøres ute i anlegget. For å kunne håndtere all denne informasjonen på en trygg måte hadde operatørene i kontrollrommet hjelp av datamaskiner som kunne gi en prognose over hva som ville skje når en endret på enkelte innstillinger av prosessutstyret.



De viktigste justeringer som ble gjort fra kontrollrommet var:
- Justering av gassens tørrhet. Dette ble gjort ved å endre temperaturen i glykoltørkeren. Vanninnholdet i gassen som ble eksportert til Skottland måtte ikke være over 67,5 ppm, dvs. 0,00675 %
- Justering av strømningsraten på gassen som gikk inn i rørledningen til Skottland. Dette ble gjort ved å endre å innstillingen til strupeventilen på hver brønn
- Justering av trykket på gassen som gikk inn i rørledningen til Skottland. Dette ble gjort ved å endre strømningsraten. Gassen som British Gas Corporation mottok skulle alltid være på 44 bar. Derfor måtte trykket ut fra Frigg plattformene være på 44 bar pluss trykktapet i rørledningen og prosessanlegget i St. Fergus
- Et annet forhold en måtte ta hensyn til var at kondensatet som var blandet inn i gassen, ville skille seg ut og legge seg på bunen av rørledningene dersom strømningsraten var mindre enn fire meter i sekundet.
Da kompressorene ble installert i 1981 ble det også bygget et eget kontrollrom for disse på TCP2.
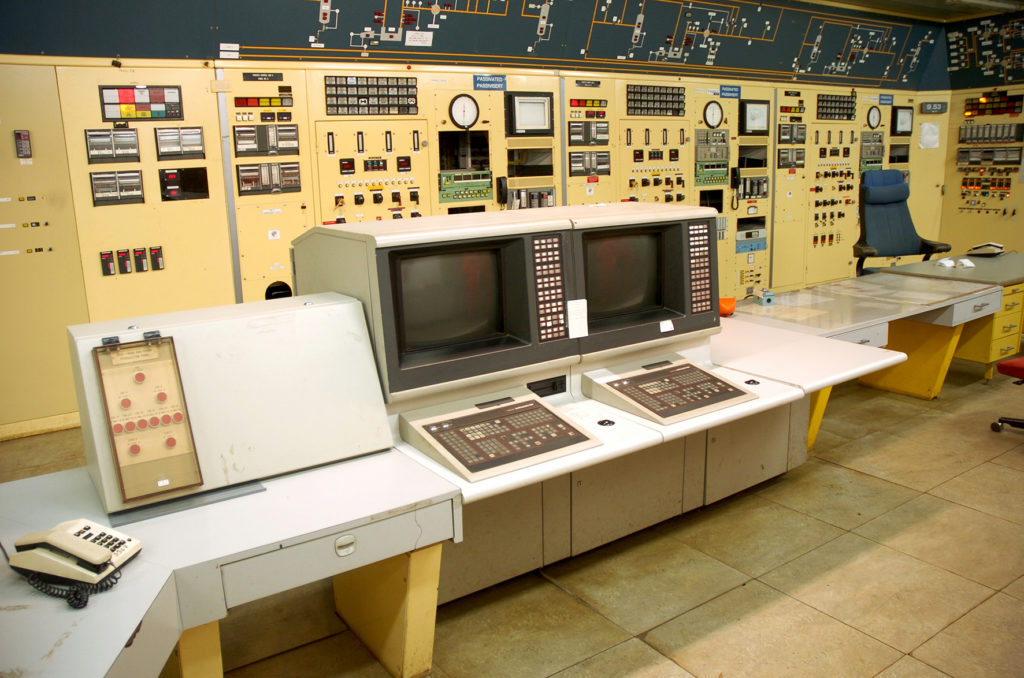