Everyday life and work

The location created a very special setting for life at work. Frigg can best be described as a separate community which existed in parallel with society at large. It became a second home to many of those employed there. In addition to being workmates, people also lived cheek by jowl.
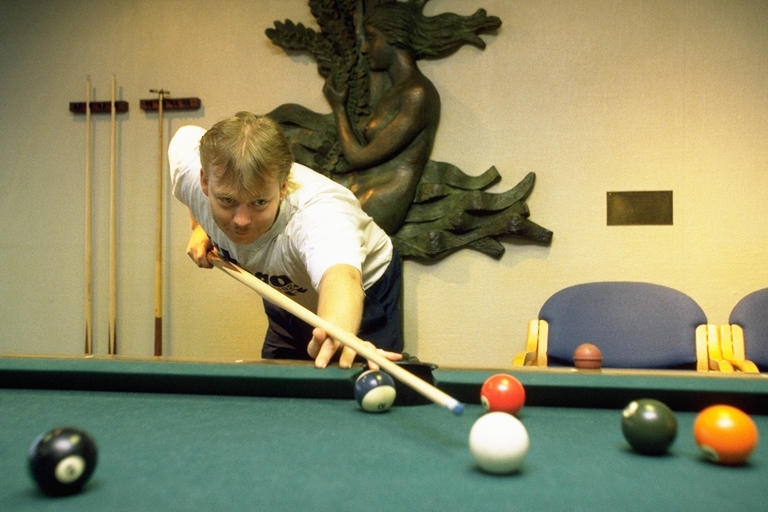
Life offshore consisted mainly of working, eating and sleeping, as well as a few hours for leisure activities. Contact with family and friends on land was limited to phone calls or letters. The transition from home life to the Frigg community and culture began with the flight offshore. By donning a survival suit and boarding the helicopter, people left their shore lives and re-focused on the culture and community of this second home. They stayed remote from happenings on land until the survival suit was shed on their return.

Frigg had many features in common with the other platform complexes on the Norwegian continental shelf. Workplaces and accommodation were virtually identical everywhere. The same system of offshore tours, with a long period of work followed by lengthy spell of free time, was practised throughout the North Sea. But the environment and working conditions on Frigg nevertheless had some special features, a distinctive social setting. The oil business in Norway was characterised during its early phase by an Anglo-American culture, with the US majors dominating. Frigg had a French operator, and thereby a leadership with a Gallic work and management culture.
Stories were told from other fields about Norwegian workers who were fired one day and threatened with the first helicopter home, before being forgiven the following day. That leadership style was unknown on Frigg. The French management had different ways of making its authority felt. This culture also influenced the Frigg community in other ways.
So what were working conditions and everyday life like on the platform complex straddling the boundary between Norway and the UK and operated by a company from France?
A job on Frigg also had a number of features in common with industrial workplaces on land – a refinery, for instance. That relates particularly to the technology employed. But it also had numerous parallels with shipping, another 24-hour society. Construction work was characterised by commuting and changing workforces as assignments such as development or drilling were completed. That applied especially to personnel from contractor and service companies.[REMOVE]Fotnote: Karlsen, Jan Erik, Arbeidsvern på sokkelen, Universitetsforlaget 1982.
Even with a workplace far from home, opportunities existed for daily contact with the wider world through phones, newspapers and TV. These improved over time. In the early years, getting a phone line to land was difficult and no direct TV transmissions existed.
Patrice de Wangen, who worked on Frigg from 1980, reports: “It could be difficult to begin with. We only had a limited number of lines then. There were phone booths. If you were delayed, you ran the risk of not getting a line until very late. After 10 minutes, the pips sounded and you had to hang up. Contact with land wasn’t easy, and the community became a bit isolated.”[REMOVE]Fotnote: Interview with Patrice de Wangen.

The installation of more phone lines in the 1980s, and not least the arrival of satellite TV, made a marked difference to opportunities for participating in life ashore. Although phones were never installed in cabins, open lines became available in the offices. It was never hard to get a line out. The internet and e-mail also provided opportunities for most people. That helped to narrow the distance between life at work and at home.
Frigg employees could find that their workplace seemed remote to families and friends on land. It was hard to envisage what life was like on the platforms. So Elf organised “wife excursions”. Spouses flew out on a day trip by helicopter, and tours were organised to show them what the place was like. Known as “pink flights”, these outings were staged in the spring when the weather was at its best. They became very popular.[REMOVE]Fotnote: Interview with Patrice de Wangen.
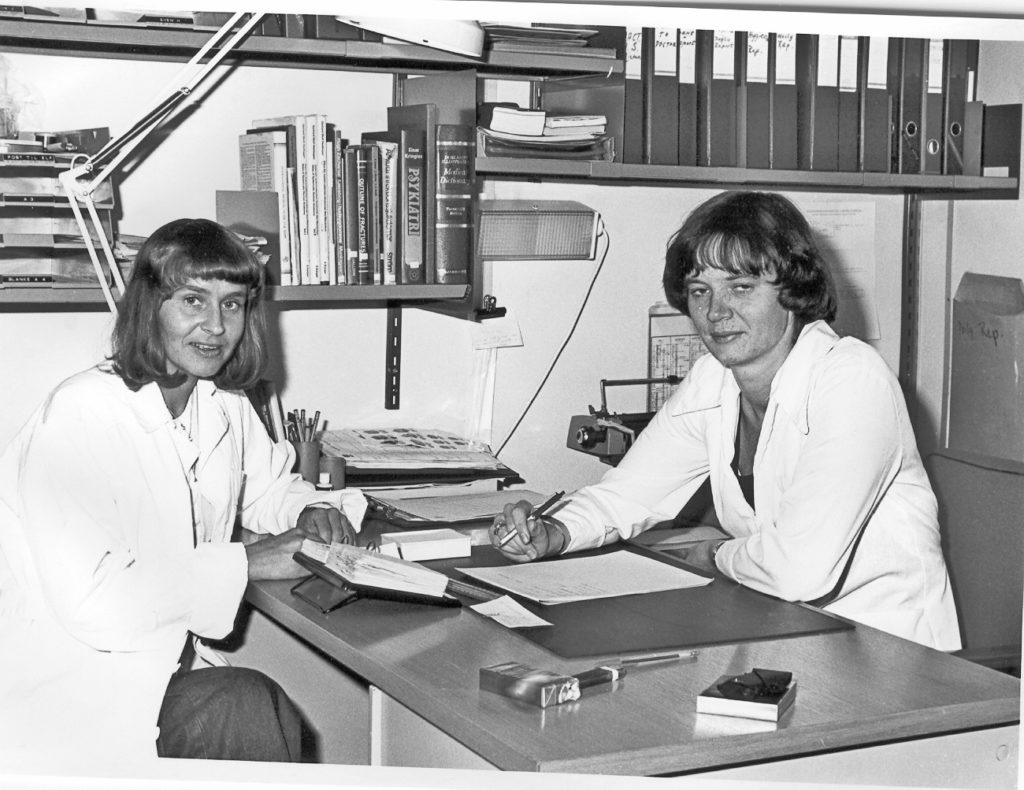
Women came early to Frigg, but remained a minority. The field acquired the first permanent female employee on the NCS in 1978, when Svanhild Rolfsen arrived. She recalls: “I was the only woman to start with, and I actually only have good memories of that time. More arrived eventually, but there were never many of us.”
Views on women offshore were divided, but they soon became a natural part of life on the platform, as Rolfsen observes. “To begin with, some of the workers were sceptical about female nurse. They probably wondered a bit about what type of woman could join this “masculine society”, but it didn’t take long before I was accepted … A lot of men weren’t used to seeing women out on the field, but such attitudes disappeared over time. Many undoubtedly appreciated that the field became more like an ordinary community rather than a rough male society. Elf was good at facilitating conditions for women, and its emphasis was on competence. Changing rooms and other facilities were provided for both sexes. When I arrived on the field, conditions were better than I’d expected.”[REMOVE]Fotnote: Interview with Svanhild Rolfsen.
Offshore installation manager Christian Hansen on Frigg confirms this picture: “It’s correct that facilities for women were made available from an early stage. One thing which happened when the women came out was that people washed more frequently. The Frenchmen were dubious about having women offshore, since they thought it would create unrest and problems.”[REMOVE]Fotnote: Interview with Christian Hansen.
Shifts and reliefs
Production continued around the clock on Frigg. The process never stopped, and everyone worked a 12-hour shift. A number of jobs, primarily production, catering and communications, involved both day and night shifts. The working day ran from 07.00 to 19.00 for the day shift, and from 19.00 to 07.00 for the night crew. Nurses had fixed working hours during the day, but were on call around the clock. Being in reserve the whole time for 14 days at a stretch was a strain both mentally and physically.[REMOVE]Fotnote: Interview with Svanhild Rolfsen. Maintenance personnel worked only during the day.
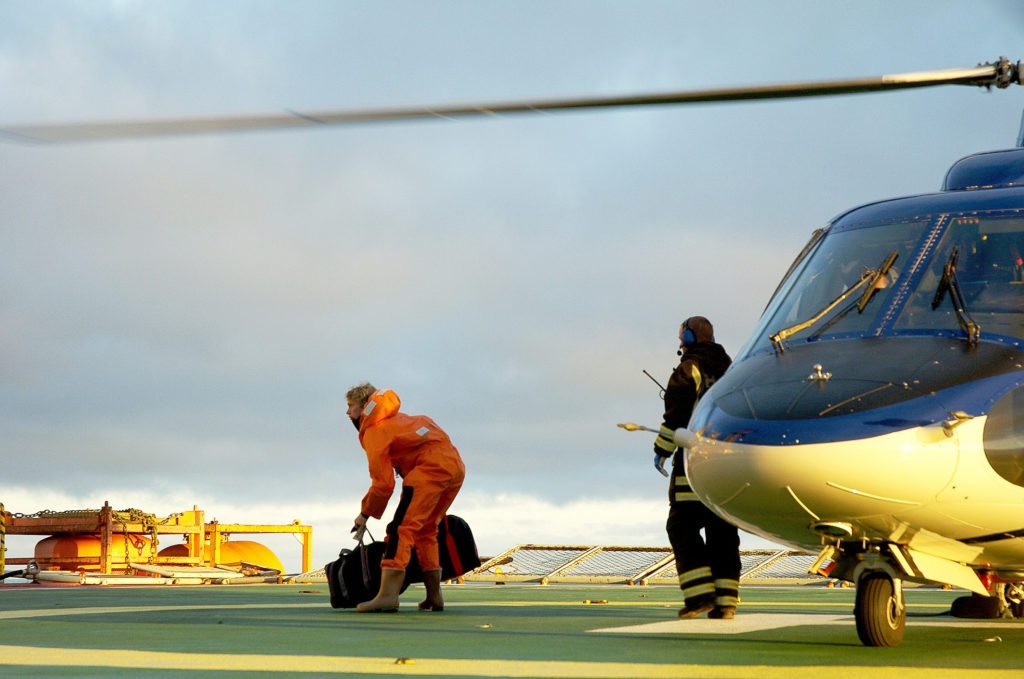
The length of an offshore tour compared with time spent on land varied during Frigg’s history, but the tend has been towards increasing leisure. When the field began production in 1977-78, most people worked eight days on Frigg and then had eight days off ashore. That changed to two weeks at work and two weeks free, and then two weeks on, three weeks off. Towards the end of the production period, time on land had risen to four weeks with 14 days offshore.
These transitions between day and night shifts and between offshore tours and periods on land led to constants changes in personnel. Much time was devoted to communicating between the different tours/shifts through reporting and log-keeping. To ensure the best possible communication, overlapping was practised between certain functions – in other words, a tour team was gradually relieved rather than everyone being replaced on the same day.
Safety and working environment problems or other issues affecting the workplace were largely resolved at a weekly safety delegate meeting, where all work teams were represented. Elf required every contractor to have its own safety delegate while it was working on Frigg. Also present were Elf’s chief safety delegate, a management representative and the nurse. These meetings were part of the safety philosophy on Frigg.
Jan Erik Karlsen, head of research at Stavanger’s former Rogaland Research institute, highlights the safety delegate meetings on Frigg in his book on offshore occupational safety.[REMOVE]Fotnote: Karlsen, Jan Erik: Arbeidsvern på sokkelen. Arbeidsmiljø, faglig strategi og vernesamarbeid i oljevirksomheten. Universitetsforlaget 1982. p 204. He maintains that they were the most important forum for problem-solving. Although the meeting had no legal status and accordingly did not qualify as a working environment committee, all important safety and working environment issues were discussed there. Cases of common interest were solved quickly and without major frictions.
Ragnar Fanebust, chief shop steward in the former Norwegian Oil and Petrochemical Workers Union (Nopef), has also said that the safety delegate meetings functioned well for both safety and working environment issues. According to him, the system of weekly meetings where everyone was represented unquestionably provided the best solution for safety work by comparison with any other offshore field in the world. “We have an example here of what can be achieved when the employer meets us half-way.”[REMOVE]Fotnote: Ragnar Fanebust in “Verneombudet, tillitsmannen og fagforeningen fra 1981”, referred to in Karlsen, Jan Erik; Arbeidsvern på sokkelen. Arbeidsmiljø, faglig strategi og vernesamarbeid i oljevirksomheten. Universitetsforlaget 1982. p 204.
Safety
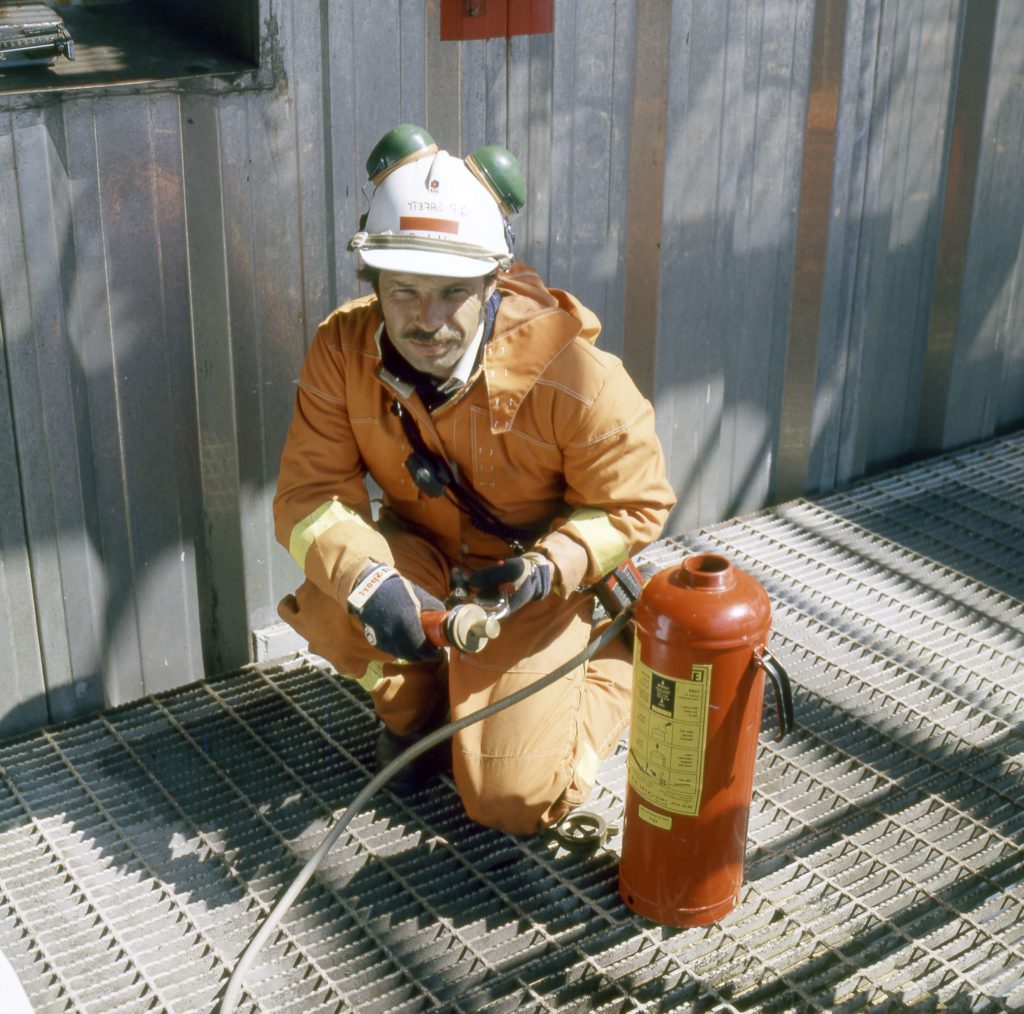
Viewed from outside, the Frigg workplace could appear hazardous. Working offshore always involved a certain level of danger, not least because people were transported to and from land by helicopter. Safety accordingly had a high priority.
Rolfsen believes Elf took safety seriously from the start. “I’m proud that my employer has had such a fine safety attitude from an early stage. In my view, we’ve avoided many injuries and incidents because of that. I’ve now worked offshore for 29 years, and don’t think I could have stood it if I’d felt that safety wasn’t a top priority in my workplace.”[REMOVE]Fotnote: Interview with Svanhild Rolfsen.
The workforce lived and slept on the quarters platform (QP), which stood some distance from the gas flows and processing facilities. Many also worked on this installation. Unlike a lot of other platforms on the NCS and the wellhead platform on Frigg, where the quarters module stood on top of or close to the processing plant, workers in the complex could sleep safe in the knowledge that no highly flammable gas was flowing right underneath them. As an extra precaution, a firewall was installed on TP1 where it faced QP to prevent a possible blaze from spreading.
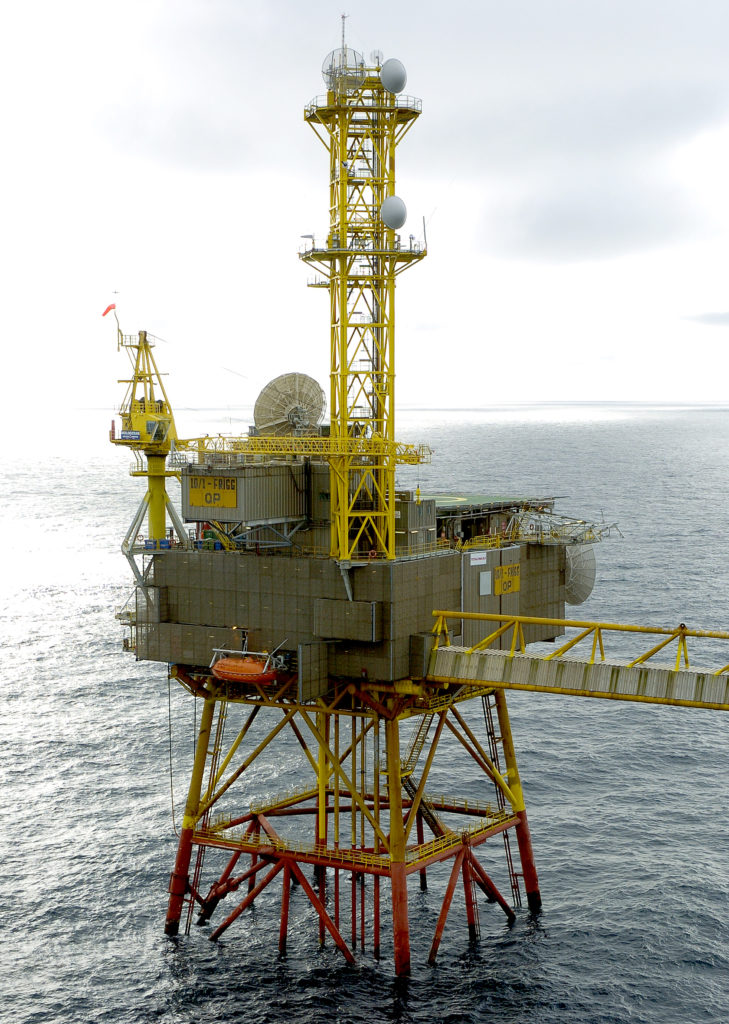
Although safety was always in focus, everyone who worked on Frigg was aware that a potential threat of a blowout, explosion or fire would always exist. Highly flammable gas came up under high pressure, and it would not take much for everything to blow up. This meant that safety thinking was always at the forefront for the workforce. A series of incidents reminded people about the forces which had to be kept under control.
A fire broke out in 1992 in a methanol cabinet in one of the TCP2 shafts. Because procedures were observed, this blaze was brought under control after 90 minutes and never developed into an acute threat to those present. But such an event brought home how easily uncontrolled incidents could occur. Had the fire spread to the gas flow arriving under high pressure from the wells, it could have caused a disaster. Everyone working on Frigg was aware of what had happened on Britain’s Piper Alpha gas platform in 1988. This installation was tied into the UK gas pipeline from Frigg to St Fergus. When it exploded as a result of a gas leak, 167 people were killed.
Processing facilities
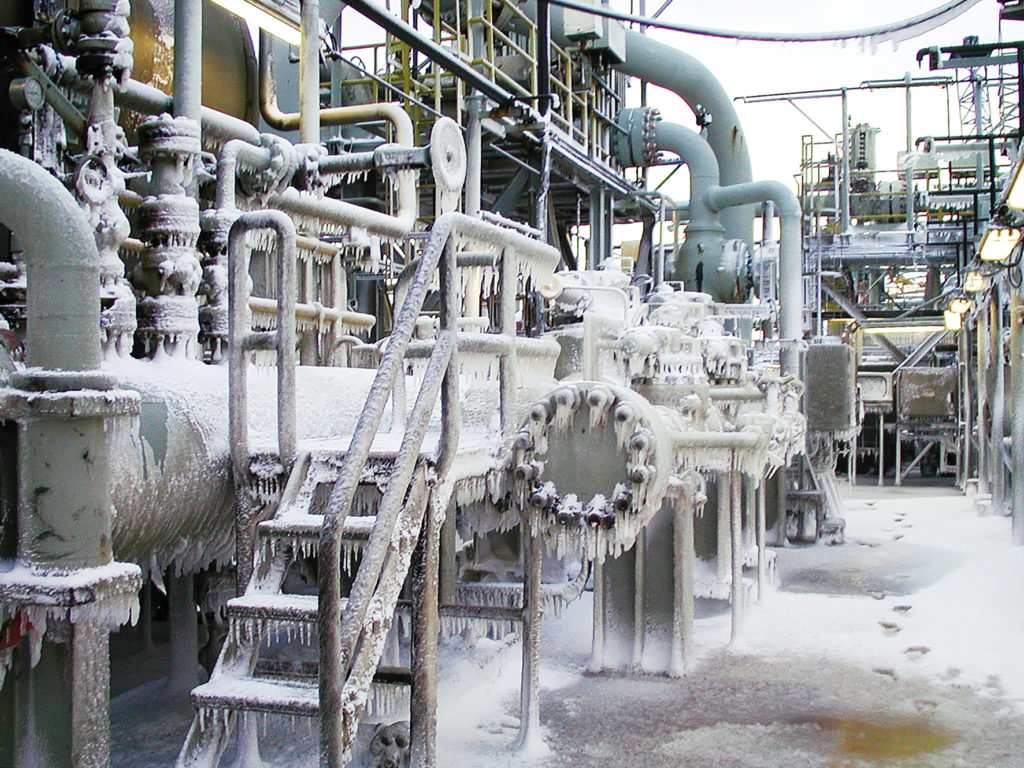
Operators on Frigg constantly faced fresh challenges as a result of new developments and tie-ins to the production process. “We mustn’t forget that Frigg has consisted of far more than the main field,” observes Torbjørn Olsen, an operator on the field since 1977. “North-East Frigg, Odin, Alwyn and East Frigg were tied in. After Odin and North-East Frigg had ceased production, Lille-Frigg and Frøy were brought on stream. A lot happened all the time on Frigg, and it ended up as a big process. Lille-Frigg was a subsea development with a pressure as high as 7-800 bar, for instance. That presented special challenges.”[REMOVE]Fotnote: Interview with Torbjørn Olsen.
The production process continued by and large without major problems on Frigg. As a result, the operators could appear to have a straightforward and occasionally monotonous job. A number of them found that much of their time was spent waiting for orders from the central control room on QP. Although production operators might have little to do at times, however, they were expected to show independence of mind and an ability to make quick judgements if faults occurred with any of the equipment. They had to respond very swiftly and accurately on such occasions.
Monotony at work was a safety hazard. Important changes might be overlooked. Even small variations could be highly significant.
The processing facilities on Frigg were managed from a control room on QP. To secure variation in the working day and to ensure that operators had an overview of the whole Frigg process, a number of them rotated between different workplaces. They spent periods in the production complex, swapping between process plant and control room. At other times, they worked on the wellhead platforms.
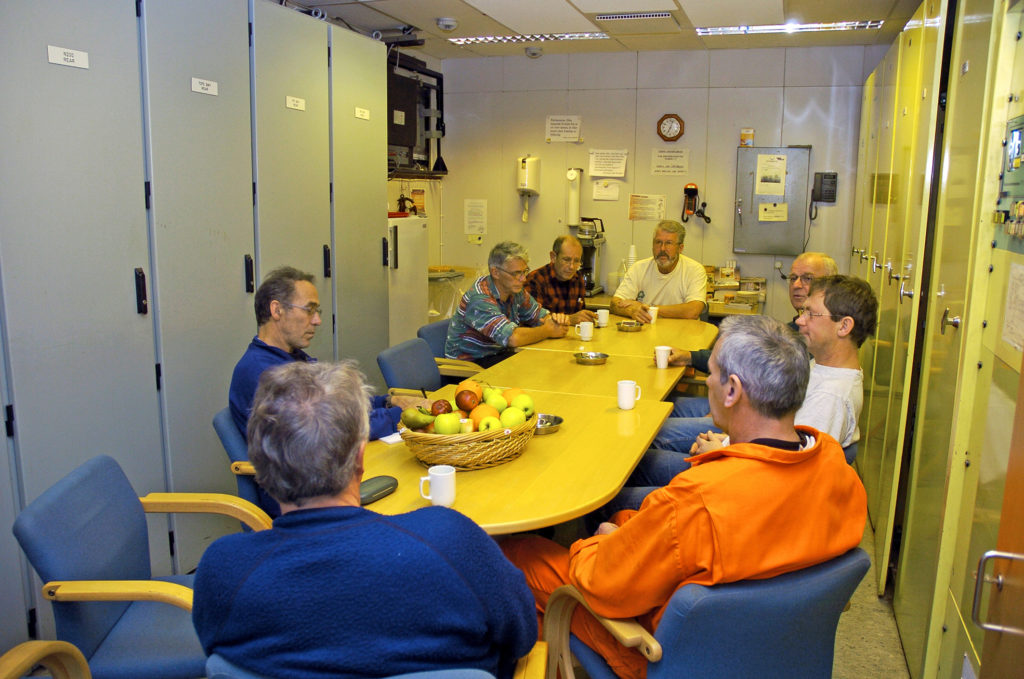
Coffee breaks were socially important. They were held at fixed times in the QP control room, reports Torbjørn Olsen. “The coffee breaks were at 09.00 and 15.00. That was when people got together, with the electricians and mechanics also dropping in. Many didn’t like work-related talk during these breaks, but they provided a great opportunity to raise problems on busy days.”[REMOVE]Fotnote: Interview with Torbjørn Olsen.
If somebody needed an extra break, coffee and fruit were always available. Coffee points had also been provided out in the process plant. A number of the operators were able to cultivate their hobbies, from knitting and writing to carving, during quiet periods when they merely had to keep an eye on things.
Language and cultural differences
A special feature of Frigg was the presence of three nationalities, with different cultures and languages. The field straddled the boundary line between the UK and Norway, and the operator was French. Communication challenges related to cultural variations, language differences and organisational divisions.
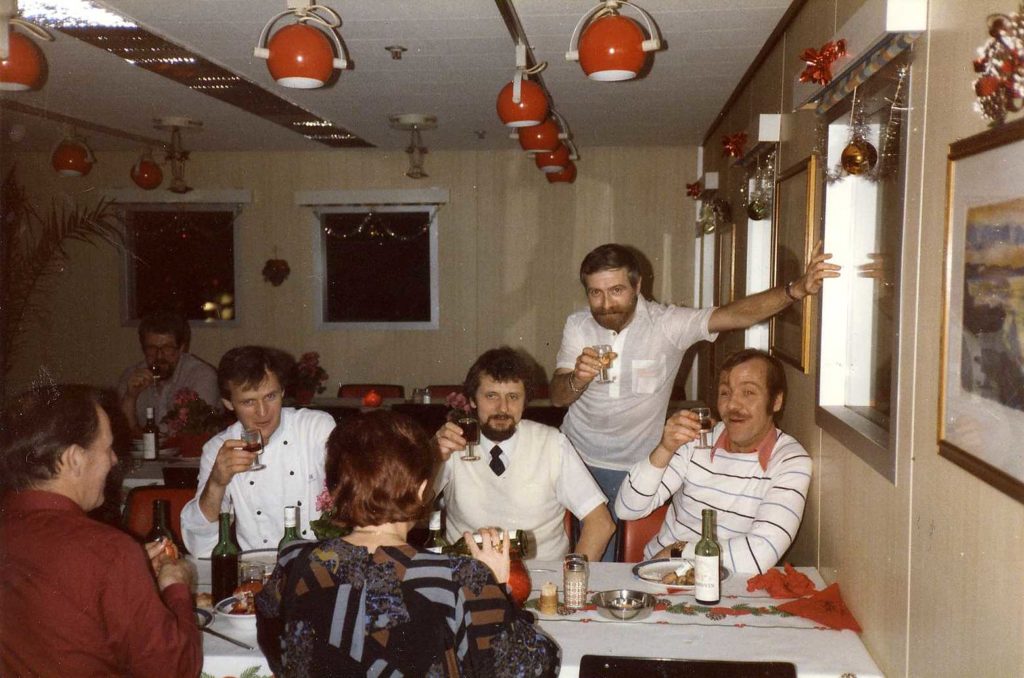
English was the official language, since that seemed the only viable option for an organisation comprising French, British and Norwegian workers in an industry where an Anglo-American tradition had become dominant. In practice, both French and Norwegian were used – particularly when speaking but also in writing.
A number of the French personnel were initially unable to speak English, and so communicated with each other largely in their own language. That severely restricted communication between the French platform management and the Norwegian workforce. A Norwegianisation process occurred during the 1980s. The management became Norwegian, and the division between Norwegian and French culture weakened. But differences did persist, and manifested themselves in various ways.
“A total of seven-eight nationalities could be present,” recalls Hansen.[REMOVE]Fotnote: Interview with Christian Hansen.“One distinction was that Norwegians took things very calmly. When a problem arose, they could sit quietly and think until they had solved it. The French became more hysterical, and leapt around. But the Norwegians usually arrived at a solution just as quickly. The British were somewhere between these extremes. They are polite, and the French fairly polite.”
The British seemed to manage fairly well in relation to both Norwegians and French. They had a particularly strong presence on the CDP1 wellhead platform, but were more thinly spread on the other installations. That helped to determine how the various nationalities interacted. The British turned up by and large to every meal, ate together, and played snooker in their free time. The French played cards. Since Norwegians formed the great majority, they divided to a greater extent by job. Creating unity in such a setting represented a challenge.
“Differences between the various nationalities became less marked over time, but they were still there” says Rolfsen.[REMOVE]Fotnote: Interview with Svanhild Rolfsen. “That included attitudes to women. If a woman is carrying something heavy, a Briton will normally offer to take it for them, while a Norwegian will just say “hi” as they sweep past. We had a French management in the early years on Frigg, which didn’t initially understand the safety delegate system. They found it incomprehensible that an ordinary worker could stop hazardous work simply because that person was a safety delegate. Eventually, however, they came to value the system. All in all, the French management has been very good. It’s been part of the Frigg culture to speak out to management. Everyone on the field wore a white hard hat, regardless of their position.”
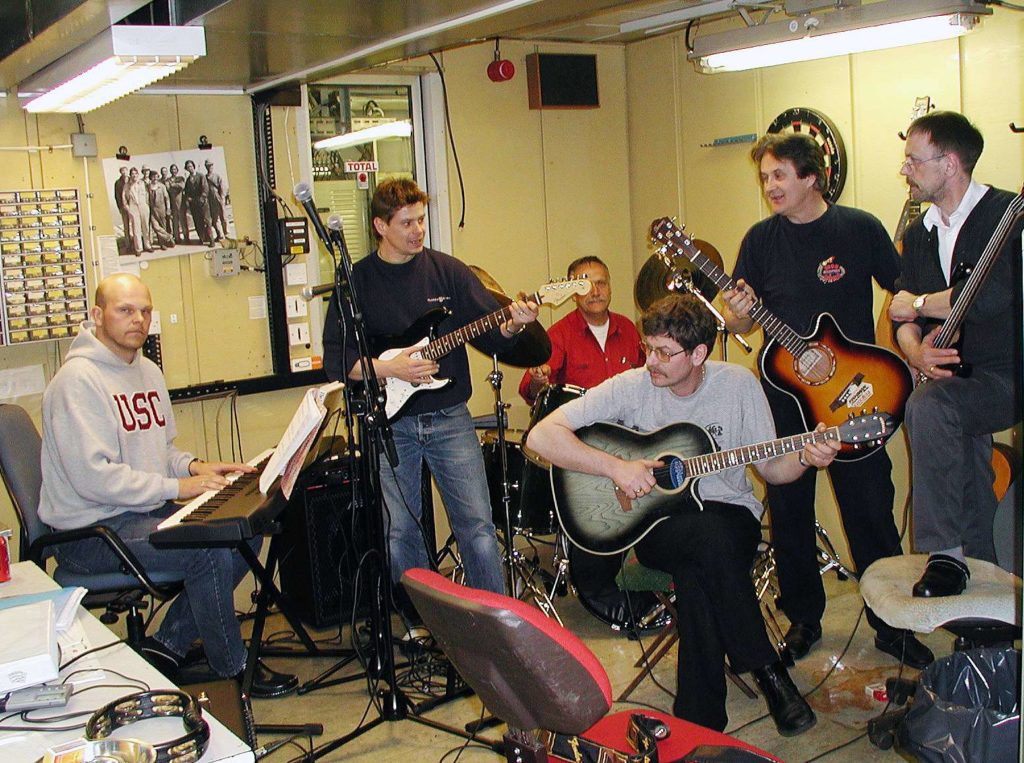
One characteristic feature of working life on Frigg was the sense of solidarity and loyalty to the field and to operator Elf. The solidarity arose partly from the isolation of the workplace and the fact that the same people were together on each tour. They were concentrated in a small area, with no opportunity to withdraw. That left little or no room for a private life. The same workers spent much of their lives together, both at work and in the limited free time they had offshore.
Loyalty to the field and respect for Elf applied not only to the operator’s own employees, but also to contractor personnel. As mentioned above, the latter were represented on equal terms along with everyone else on the platforms at the safety delegate meetings. But contract workers were also included in other ways.
Erling Hellesund, an ESS steward and a contractor employee on Frigg for many years, describes his perception of the community as follows: “The sense of community on Frigg was very good, and collaboration with Elf quite fantastic. You were never bounced off a helicopter flight because an Elf employee needed to go offshore or to land, which could happen elsewhere. All welfare provision extended to every permanent employee on the platform, and not just Elf staff. When Elf celebrate an anniversary, catering personnel and other permanent workers on Frigg were invited and had their travel and accommodation expenses covered for themselves and their spouses. Permanent catering staff on Frigg were included in the Elf/Total bonus scheme and received a final payout of NOK 20 000 on equal terms with Elf employees.”[REMOVE]Fotnote: Interview with Erling Hellesund.
“One reason for the good community spirit was that we were largely the same people, both Elf employees and contractor personnel,” adds Olsen.[REMOVE]Fotnote: Interview with Torbjørn Olsen. “The contractors on Frigg were treated the same as Elf staff. They were treated well.”
Well-being and food
Many aspects helped to bind the workforce together, regardless of nationality, position or company which employed them. A lot of effort was devoted to creating solidarity on Frigg. The most important single factor was food. Frigg had a North Sea reputation for good cuisine, and Elf made a big commitment in this area. French chefs were aboard from the first day until the field was shut down. The raw materials were always fresh, flown in if necessary. Special dishes were often served in unexpected settings for activities and entertainment, such as a prawn party on the helideck, Mexican evenings and so forth – not to mention such occasions as Christmas, New Year and Norway’s Constitution Day on 17 May. The Irish say that those who eat and drink together, stick together. That certainly seems to have been the case on Frigg.
A bar was also provided on QP, serving coffee, mineral water and non-alcoholic beer and wine. The day’s papers were flown in. Uniquely for platforms on the NCS, red wine was served with meals on Christmas Eve and New Year’s Eve. This helped the workforce to feel valued.
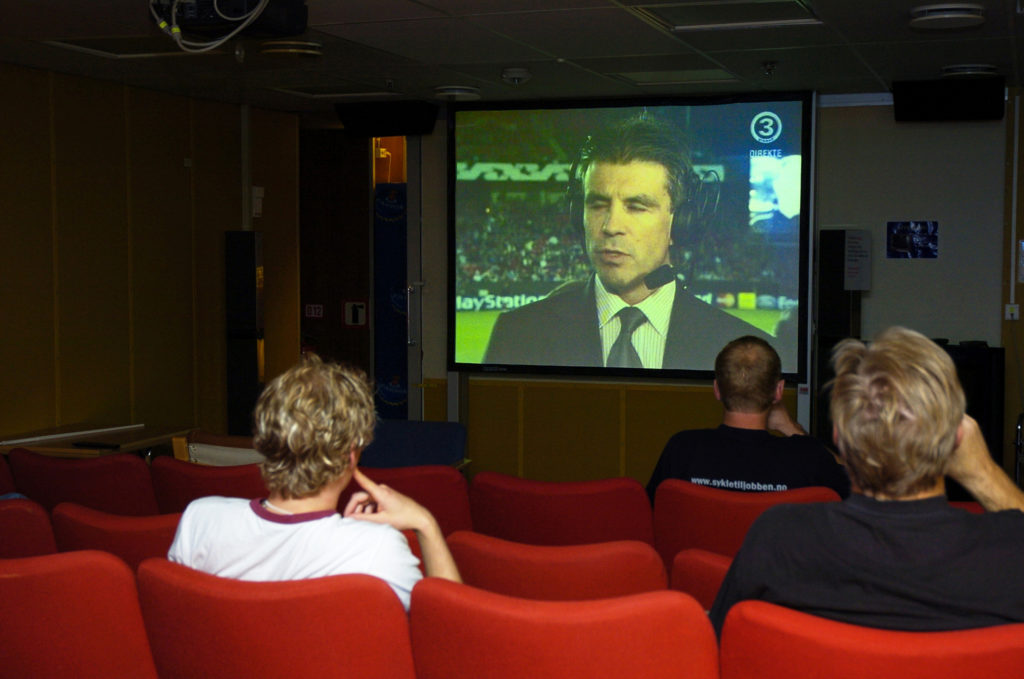
Facilities were provided for a number of leisure activities. The bingo games held every other Saturday were popular, and everyone attended. Entertainers were also flown from land. A well-equipped music room, gym and cinema were provided. Snooker, as mentioned above, and darts were popular leisure activities and the subject of competitions. That was not unique for Frigg, but applied generally to Norwegian offshore platforms.
The way leisure time was organised on Frigg changed over the 27 years when the field was on stream. A particular change in social patterns occurred after TV had been installed in every cabin. Before that, “everyone” was in the public areas – playing snooker, cards or darts, relaxing in the bar or reading newspapers – or the cinema. Afterwards, more and more people withdrew to their own cabins. Many feel that this weakened social life and solidarity. Others would argue that it was good to be able to relax in one’s own cabin, without being forced to be social all day. When people lived and worked as closely together as they did on Frigg, it could be good to have an opportunity to withdraw.
“This was a very disciplined community, and people had nowhere to be alone,” observes Rolfsen.[REMOVE]Fotnote: Interview with Svanhild Rolfsen. “You flew out together, lived together, ate together, sat in the recreation room together, in the gym, the smoking room, at work. Other people were everywhere, in fact. I’ve decided that an offshore worker has to be a very flexible and tolerant person to cope with all this. It’s not surprising that you’re pretty tired and worn out after a 14-day tour.”
As mentioned already, Frigg had many features in common with workplaces on other platforms. Everyone who works offshore is away from family and friends for extended periods, is involved in a business which continues around the clock, and must accept that they are in a hazardous workplace. But Frigg had its distinctive features. Elf was early in appreciating the relationship between safety and the environment. The weekly safety delegate meetings discussed all issues relating to these aspects, and measures were quickly adopted. This contributed to the sense of security felt by the Frigg workforce.
Another element highlighted on Frigg was well-being. Through food, the provision of facilities and a generous budget, a lot was done for employee welfare. This has played a part in cultivating the loyalty which most people – both Elf employees and contractor personnel – felt to both field and operator.
The distinctive community which emerged on Frigg can undoubtedly be attributed to the mix of nationalities which characterised the field. That embraced a management with a French work culture and welfare mindset, and the mix of Norwegian and British workers. This cultural blend posed a challenge for operating the field, which was successfully overcome. The special Frigg culture was created.


