Maintenance

Minor maintenance of the production systems was carried out by the operators themselves, but mechanics, instrument technicians or electricians were asked to support bigger jobs. Around 40 per cent of the maintenance department’s work was preventive. The Frigg process involved three trains, with two normally operational at any given time and the third in reserve. This made the system extremely flexible and simple to handle for maintenance personnel. If repairs or maintenance were to be carried out on an operational process train, production was simply rerouted to the reserve train.
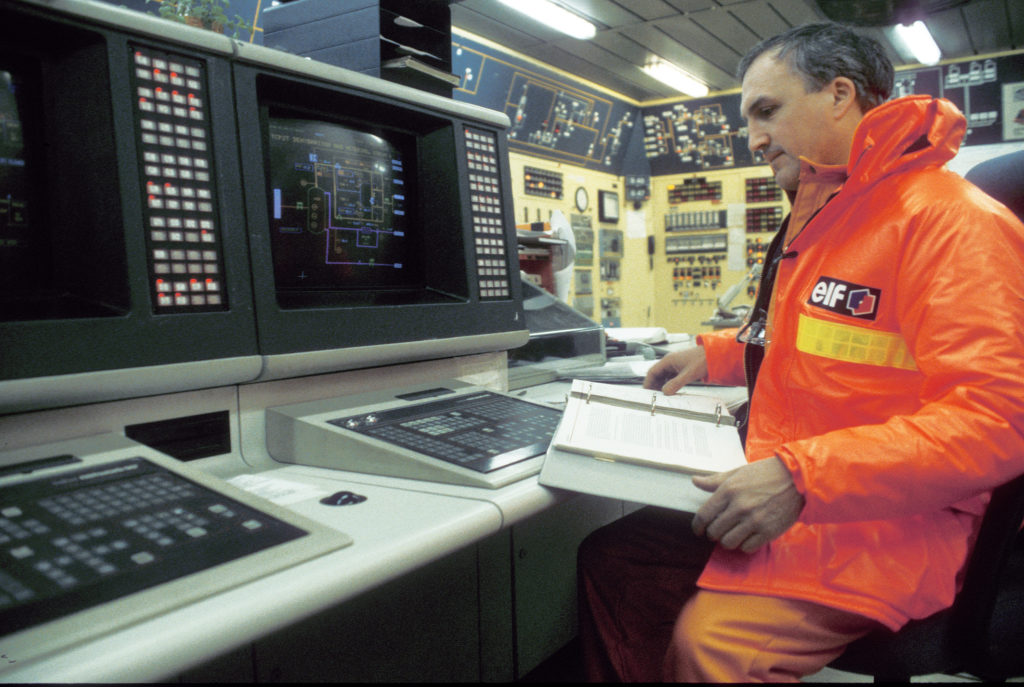
The offshore maintenance department had three groups of specialists permanently available on the platform – electricians responsible for the electrical systems, instrument technicians and mechanics. Other personnel were in charge of the compressor system, with its turbines, compressors and diesel engines. Yet others looked after the process instrumentation and automatic safety system. Dedicated maintenance personnel dealt with satellite communications, other telecommunications, radio, radar and the internal communication equipment. Electricians, instrument technicians and mechanics had their own offices on TCP2. While most of the mechanics worked for Bjørge Offshore, Elf employed the other two categories of personnel directly. In addition came scaffolders responsible for rigging and removing all scaffolding, as well as painters and sandblaster who worked all year round on keeping the platforms in good condition. These were also contractor personnel. Both drilling platforms had the same type of maintenance personnel.
A dedicated electrician was responsible for power supplies on Frigg. He was an Elf employee and a member of the maintenance department. His office was the motor control centre on TCP2. This was a monotonous job, although its duties eventually expanded as more processing equipment required electricity. Initially, a generating plant on TP1 supplied the whole field with power. After the compressors became operational in 1981, this function transferred to two large gas turbines with generators in the compressor modules on TCP2. These units were dubbed Elias and Monica. The job could be stressful at times, with seconds vital, since a failure in the electrical system could lead to a full shutdown. But it was generally uneventful. A small workshop available in the control centre was much used for various hobbies.
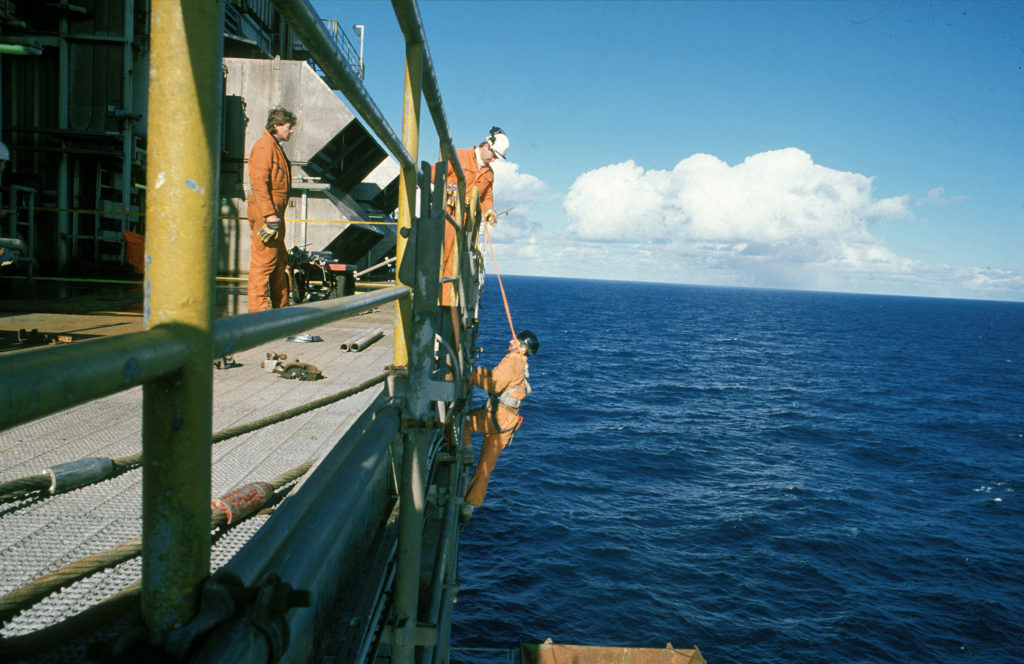
The spring and summer season was the most hectic period for the maintenance department. Production was then at its lowest level, and opportunities best for shutting down all or part of a platform. The ability to shut down various items of equipment made inspection and repair work easier and safer. Much effort was devoted to preparing for maintenance in order to ensure that downtime was as short as possible. Frigg could continue delivering gas to the UK even with one platform fully shut down. The system was so flexible that production would continue from just one drilling or processing platform.
The maintenance programme on Frigg was eventually run by a computer system with an overview of all the jobs to be done. This applied, for instance, to work on shutdown tests and preventive maintenance. Both on the Frigg complex and on the drilling platforms, the offshore installation manager summoned all the heads of the various departments to a daily meeting at 18.00, where the work for that day was reviewed and jobs for the following day notified. Everyone concerned had to know where maintenance was being carried out, particularly if it involved “hot” work such as welding. Before this meeting, the safety supervisor prepared work permits for every job, specifying the measures which had to be taken. At 07.00 in the morning, maintenance personnel came to the safety supervisor to fetch these permits. A copy had to be delivered to the control room, so that the operators knew at all times which work was being performed where. The copy then had to be retrieved from the control room when the job was over. People often failed to observe this routine properly. After a reorganisation, the production operators were made responsible for signing work permits both before they were issued and after the relevant job had been done.

